index
- Introduction to connector terminals
- Manufacturing methods for connectors
- Functions of connectors
- Materials for connectors
- Surface finish plating
- Shapes of connector terminals
- FINECS's connector terminals contributing to electrical contacts
FINECS’s connector terminals contributing to electrical contacts
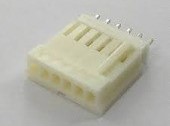
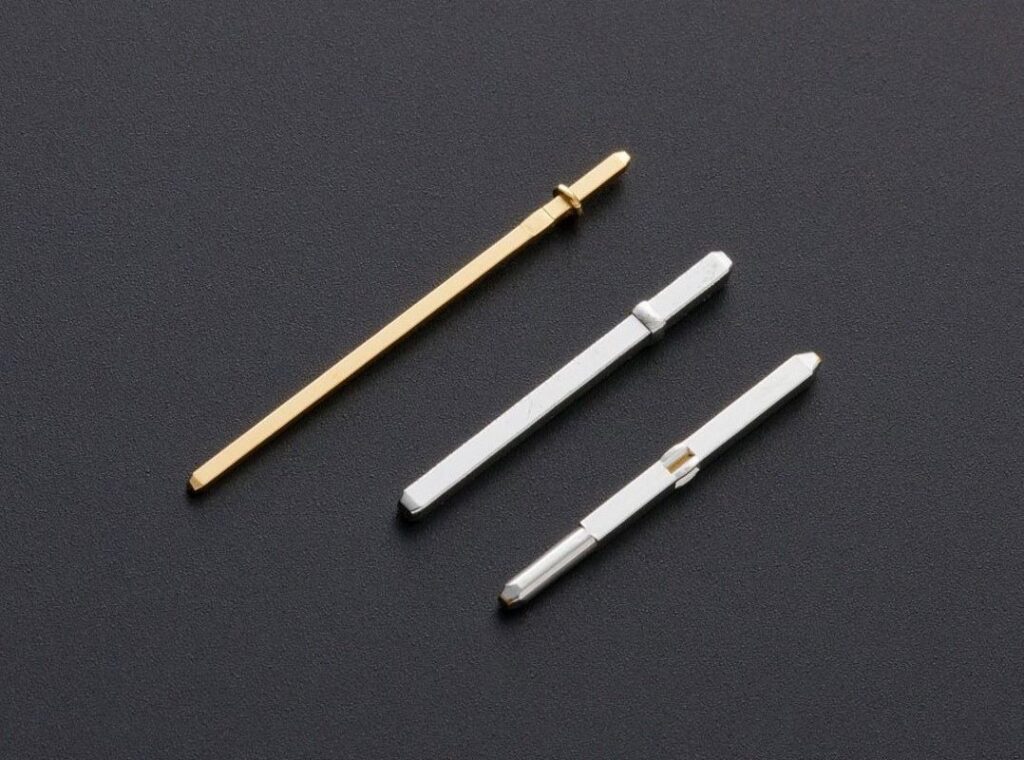
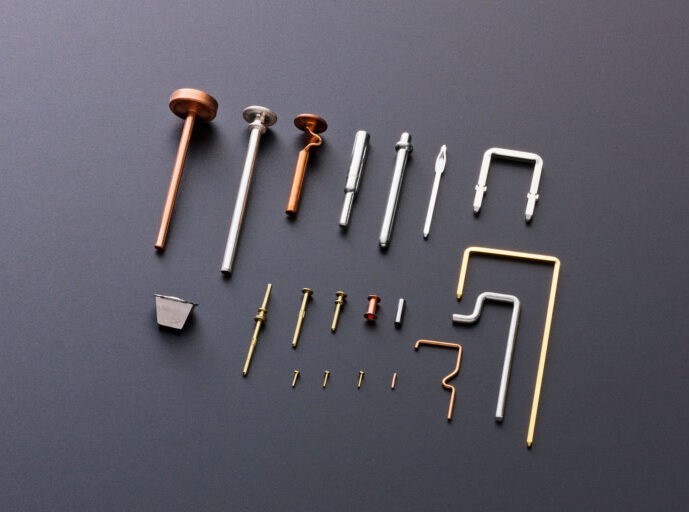
Connectors are components used to electrically connect two circuits or parts, and are included in a wide variety of products such as electronic devices,
household appliances, industrial machinery, automobiles, and telecommunications equipment. In general, there are two types of connectors: male connectors (plugs) and female connectors (receptacles).
Connecting a plug and a receptacle enables the transmission of electrical signals.
A connector generally consists of conductive parts, which are made of metal, and surrounding non-conductive parts, which are made of molded resin, plastic, or other non-conductive material.
The metal parts are referred to as “terminals,” “contacts,” etc., and they are also divided into male terminals (or posts, pins, etc.) and
female terminals.
This page focuses on the metal parts that function to conduct electricity, and further explains in detail the male connector terminals, which constitute FINECS’s main product range.
Types of male connector terminals based on manufacturing methods
Connector terminals are roughly divided into three categories by processing method, as follows:
(1) Press-formed terminals
Terminals made by press working out of metal strips (hoops)
(2) Headed (plastic-worked/ forged) terminals
Terminals made by heading (plastic working/ forging) out of metal wire
(3) Machined terminals
Terminals made by machining out of metal rods or metal wire
The characteristics of each method are as follows:
1. Connector terminals made by press working out of metal strips
Using commonly available standard metal strips (hoops), which are supplied in large quantities in the market, means that the material can be acquired at a relatively low cost. In addition, press working is a relatively high-speed manufacturing process suited for mass production. Furthermore, press working can also be used to make high-precision items,
as is shown by the fact that this method is used to manufacture terminals for narrow-pitch connectors that require high-precision processing, such as board-to-board connectors and FPC connectors used within smartphones and other mobile devices. On the other hand, this process involves the generation of punching slugs as a result of blanking the metal,
which leads to material loss and can be a cost-increasing factor.
As for plating to press-formed terminals, if a pre-plated metal strip, to which plating has been applied in advance, is used, the cut-off surfaces will not be plated, and bare metal will be exposed after the press-forming process. Therefore, if plating is necessary for the purpose of preventing oxidation or corrosion, non-plated metal strips should be used, and the plating should be applied after the press-forming process. With regard to the shapes and surface conditions, the cut-off surface by press working is apt to have fractured sections with rough surface conditions and tiny burrs on the edges.
With respect to the initial costs for the equipment, the presswork requires relatively strong and rigid dies, and high-precision dies depending on the products to be formed.
These dies tend to be significantly more expensive than wire heading dies (for headed terminals) and machining tools and fixtures (for machined terminals), which constitutes a negative factor for manufacturing products that have a short life cycle, products with uncertain demand, and low-volume production items.
In addition, press working involves relatively large force applied to the metal strips for shearing (punching) them, causing the profiles of the connector terminals to become somewhat deformed.
2. Connector terminals made by heading (plastic working) out of metal wire
Materials for connector terminals made by heading (plastic working) out of metal wire are divided into two types: plated wire and bare wire. Currently, the most prevalent method for plating wire (pre-plated wire) intended to be used for connector terminals is tin reflow plating. There are two types of undercoat that are typically used for tin plating:
nickel undercoat and copper undercoat. When bare wire is used, plating (tin plating, gold plating, etc.) is generally applied using barrel plating after the terminals have been formed.
Advantages in using wire to make connector terminals
Advantages of headed terminals are as follows:
(1) Initial cost of dies is significantly smaller than that of press dies.
(2) Equipment can be adjusted to process terminals with different lengths without having
to make new dies.
(3) Plating can be applied securely to all four sides of each terminal.
(4) Metal waste, which is typical of press working, is not generated, which contributes to reducing cost and environmental impact.
(5) Cross-sectional shape of wire drawn by dies remains in shape (cross-sectional shape of the terminal does not deform or warp).
To be more specific, the dies used with the automatic pin processing machine to form wire are smaller than those for press working and have simpler structure and configuration; therefore, the initial cost of dies can be held down to roughly one fifth to one tenth. Accordingly, initial investment costs can be significantly reduced.
As for different lengths of connector terminals, they can be handled simply by adjusting the processing machine. This is also an advantage of using wire because, in the case of press working using metal strips, it will be necessary to make new dies, or at least modify the dies.
With regard to plating, when using pre-plated wire, it is possible to maintain the plating evenly on all four side surfaces of each terminal. In contrast, in the case of press working using pre-plated metal strips, it is not possible to have the sheared surfaces plated.
As for material waste, the processing of wire does not generate punching waste as would be generated by press working.
The punching waste increases for thicker plates and with larger pitches. Although it is possible to sell the punching waste as scrap metal, the selling price is cheap.
This also means that the energy used in the process of manufacturing the material is wasted, and therefore it is not an eco-friendly production method. In the case of metal wire forming, almost the entire material is used without waste to make connector terminal products, so this method is considered more environmentally friendly.
Furthermore, in the case of press working, a large pressing force is applied to the entirety of the material strip, and the shearing force causes deformation of the cross-sectional shape of the terminal, making the finished shape vertically asymmetric. In contrast, in the case of metal wire forming, force is applied to only limited part of the wire and the generation of burrs can be minimized.
Connector terminals can be finished with smooth surfaces and almost symmetrical cross-sections both vertically and horizontally.
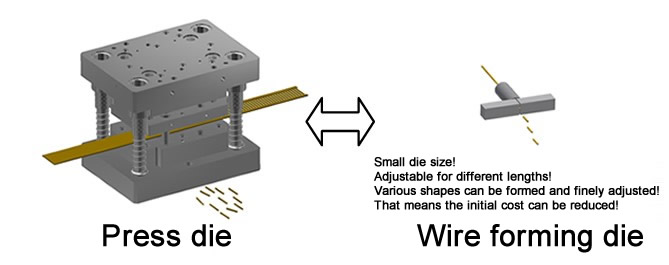
3. Terminals made by machining out of metal rods or metal wire
Machining is used for shapes and precision that can only be achieved by machining, such as processing of complex shapes and ultra high precision products.
Terminals of some special connectors are also made using machining.
Using NC lathes or special machine tools, machining can accurately achieve complex shapes that cannot be formed by press working or wire heading. However, since workpieces can only be processed one by one, the number of items processed per unit time is limited, resulting in inferior productivity.
In addition, it takes a long time to set up the equipment, and production costs tend to be high.
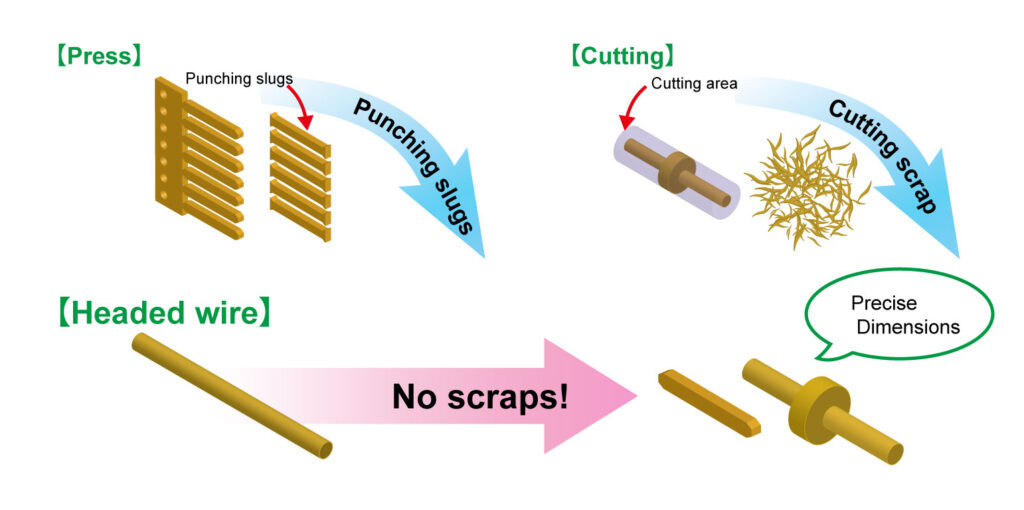
Functions of connectors
Assumed functionsof connector terminals include the following:
(1) Conductivity (transmission and supply of electric power)
- Carrying electric current
- Securing conduction capacity
- Facilitating electric current flow
(2) Conductivity (signal transmission)
- Feeding and interrupting electric current
(3) Fitting/retaining/locking
- Preventing coming-off
- Resisting vibration
- Preventing rust
- Enabling disassembly
- Enabling reuse (connection)
- Enabling reliable signal transmission through retention
Materials for connectors
Typical materials used for connector terminals are as follows:
(1) Brass: JIS C2600 (Cu 70%, Zn 29%), C2700 (Cu 65%, Zn 34%)
In terms of material costs, C2700 is slightly less expensive due to lower copper content.
(2) Phosphor bronze: JIS C5071 (Cu 98%, Sn 2%); Phosphor bronze Class 2: C5191 (Cu 94%, Sn 6%)
Used for connector terminals that require spring-like characteristics.
(3) Pure copper: JIS C1020 (oxygen-free copper), JIS1100 (tough pitch copper)
Used for terminals that require conductivity, such as power supply terminals.
Material costs are higher than brass due to higher copper content.
Surface finish plating for connector terminals
Typical plating processes for connector terminal surfaces are as follows:
(1) Tin (Sn) plating (nickel undercoat, copper undercoat)
Tin plating is the most common plating process applied to connector terminals.
Tin plating is roughly divided into two types depending on when the treatment is applied: post-process plating,
where barrel plating is applied to terminals that have already been formed using unprocessed material; and pre-process plating, where continuous plating is applied to metal strips or wire before being formed into terminals.
Methods of pre-process tin plating include tin reflow plating, which, in addition to providing a smooth surface finish, is intended to reduce the generation of whiskers by relieving the internal stress in the plated area.
(2) Gold (Au) plating (nickel undercoat)
Gold plating can be applied to the entire surface, or only to the tips (partial gold plating) to reduce the use of gold.
Gold plating is used for connector terminals that require more reliable electrical contact.
Shapes of connector terminals
Connector terminals are roughly divided into two types depending on the material wire shape:square pins made by processing square wire, and round pins made by processing round wire.
There are also partial differences in shape, and the following are some examples:
Partial forming (end forming, mid-part forming)
1. End tapering
Tapering the ends of pins enables smooth insertion or fitting to the mating part (female side, substrate).
The tapered portion can be partially rounded to reduce the insertion force and prevent scratches on the mating parts such as contacts.
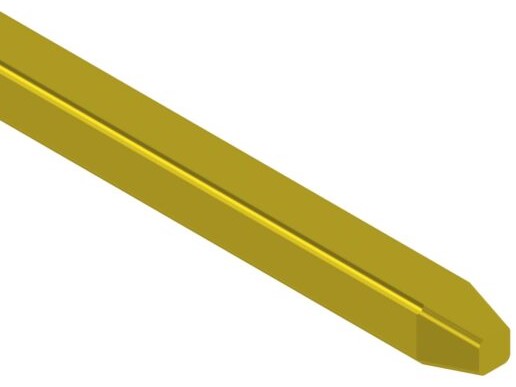
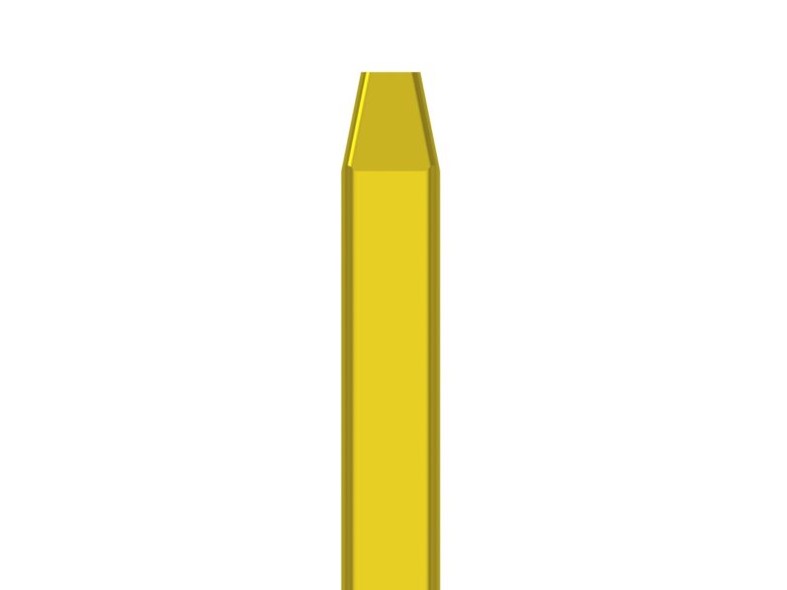
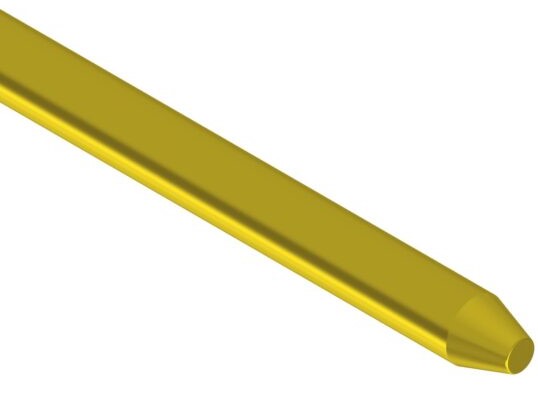
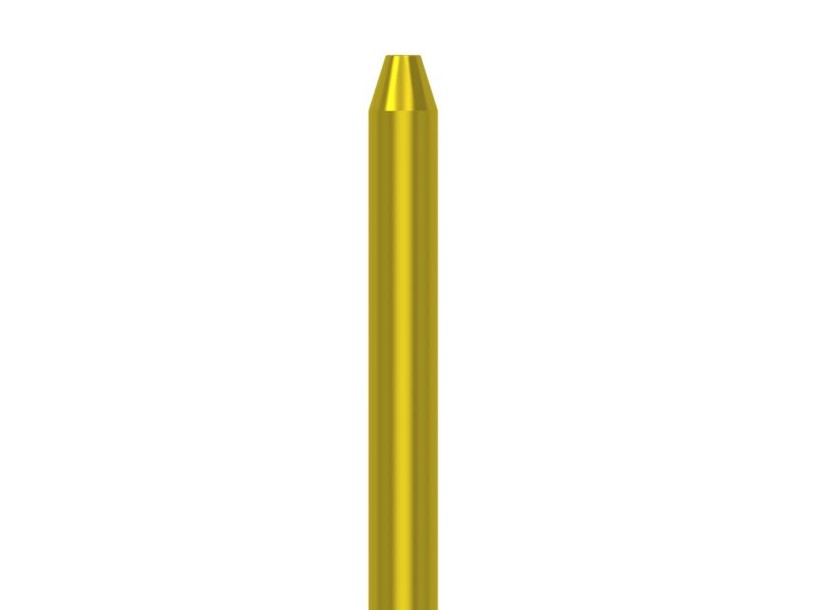
2.Straight cutting and barrel finishing
Where tapering is not necessary, pins after being cut off can undergo a barrel finishing process in order to remove sharp edges.
It is also possible to adjust the chamfering radius as needed.
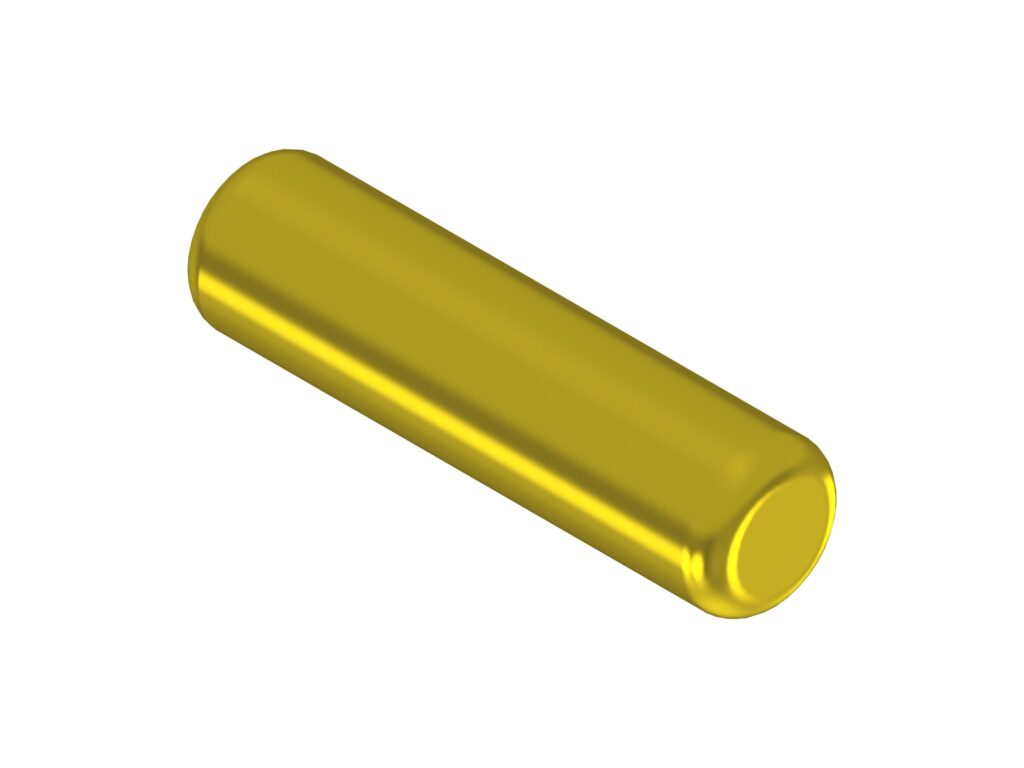
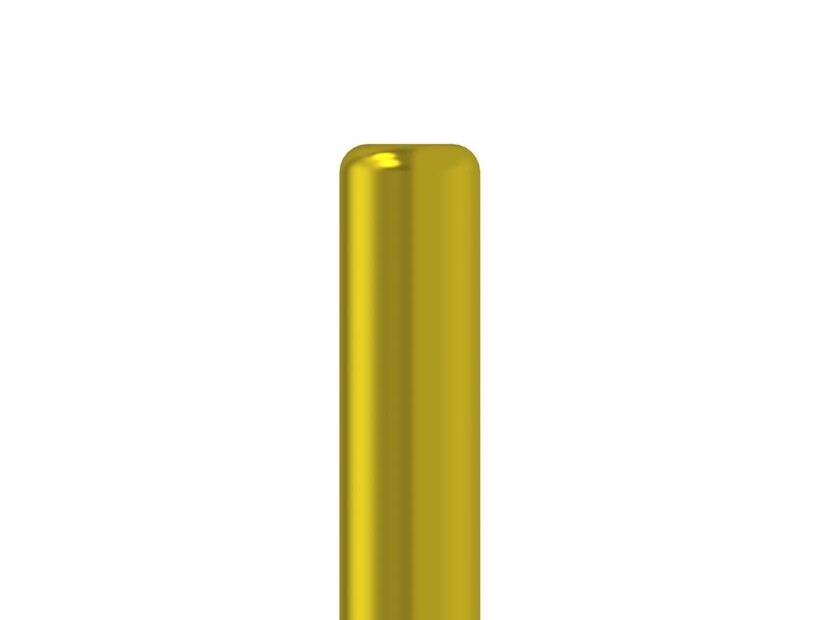
3.Mid-flange forming
The mid-flange functions to make the terminal stably fixed in the substrate or housing.
It also prevents terminals from coming out of the housing at the time of removing or attaching a connector.
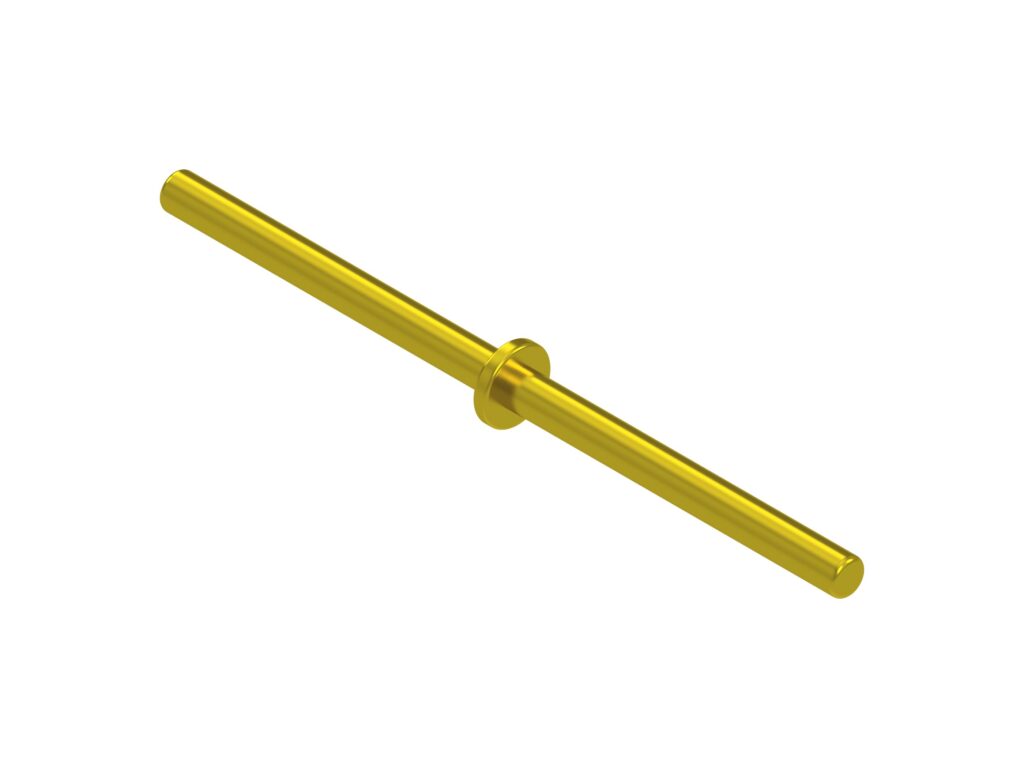
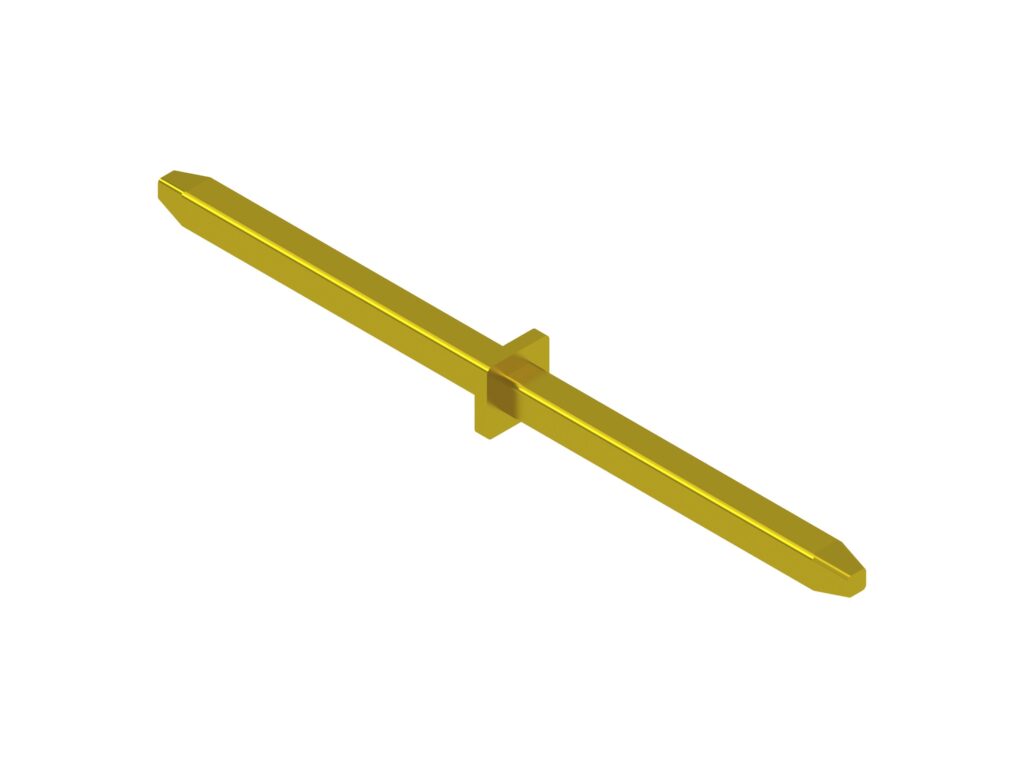
4.Press-fit configuration
The press-fit configuration allows the omission of soldering to circuit board through-holes.
There are a variety of press-fit configurations, including those patented by individual companies.
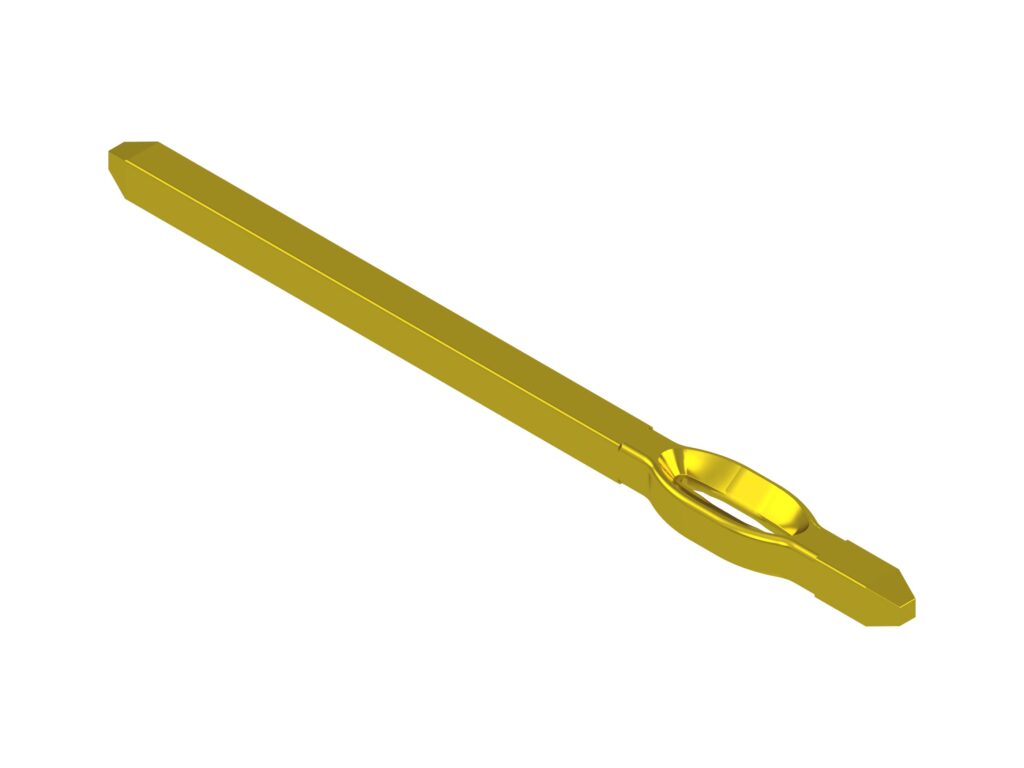
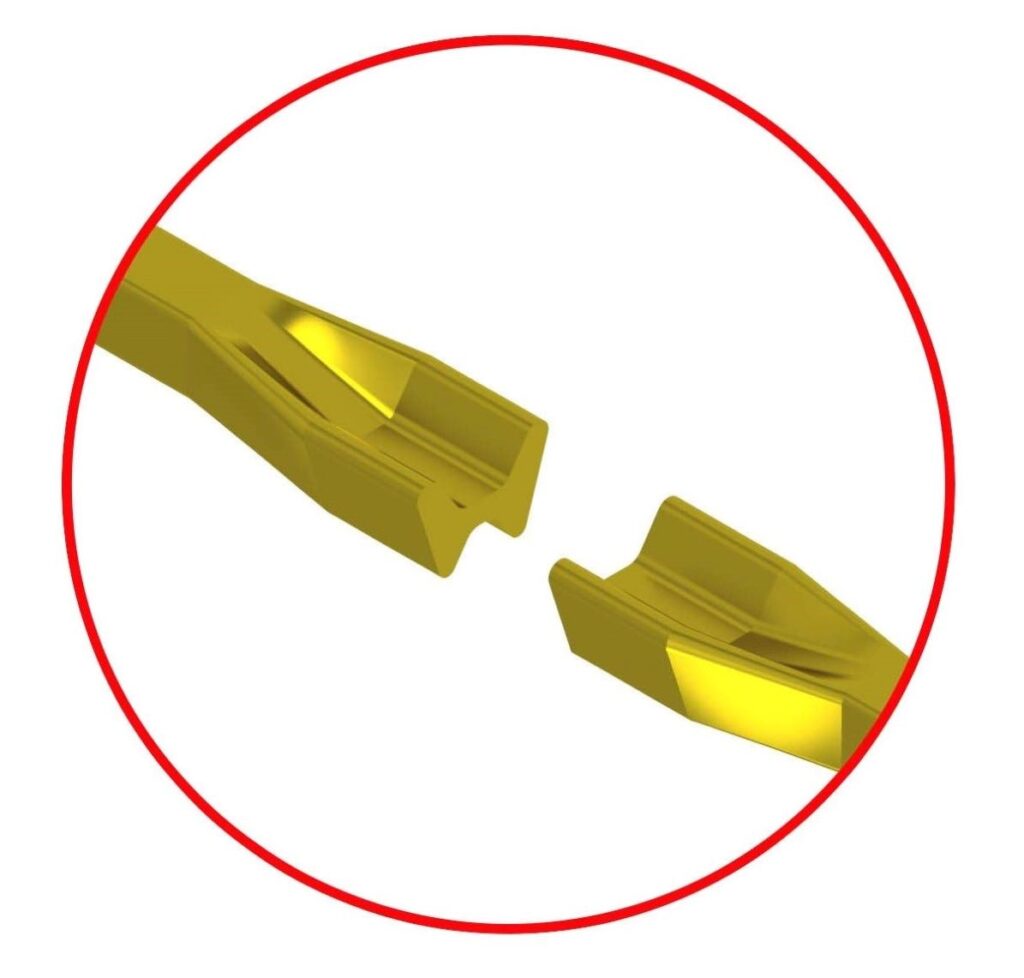
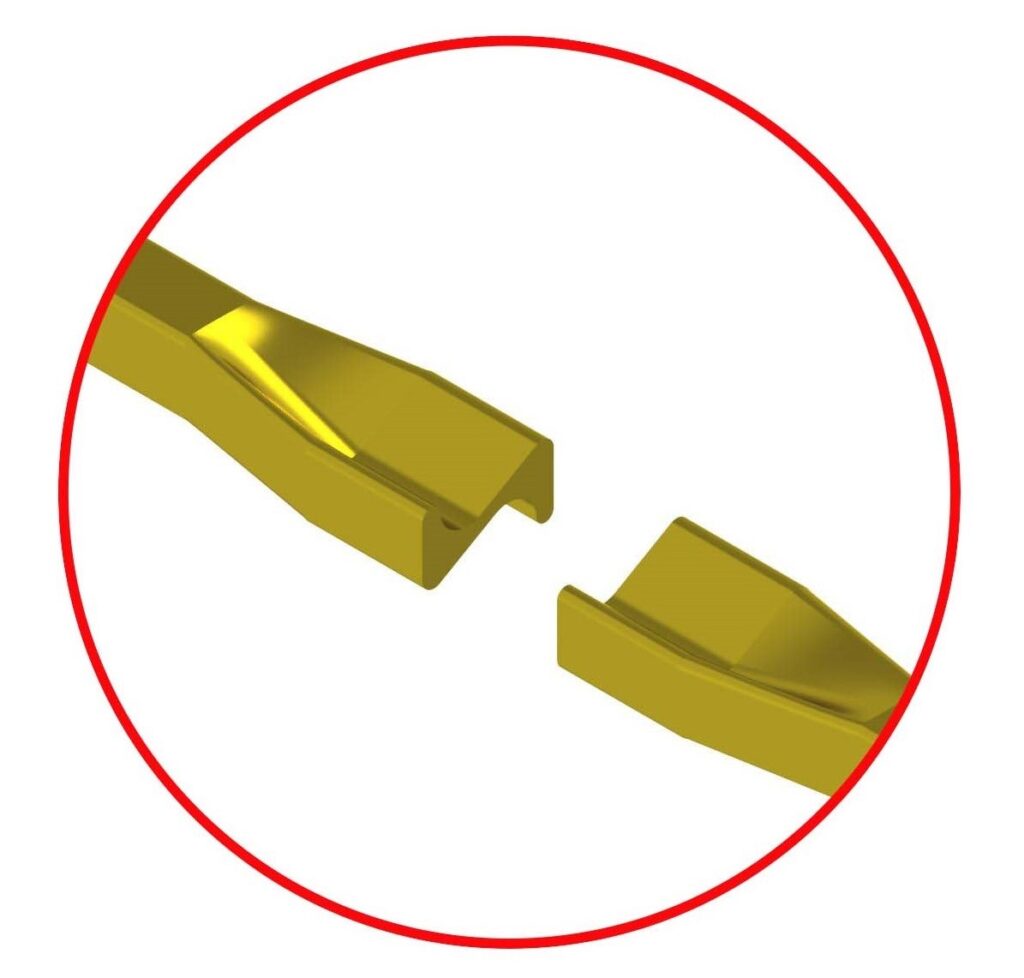
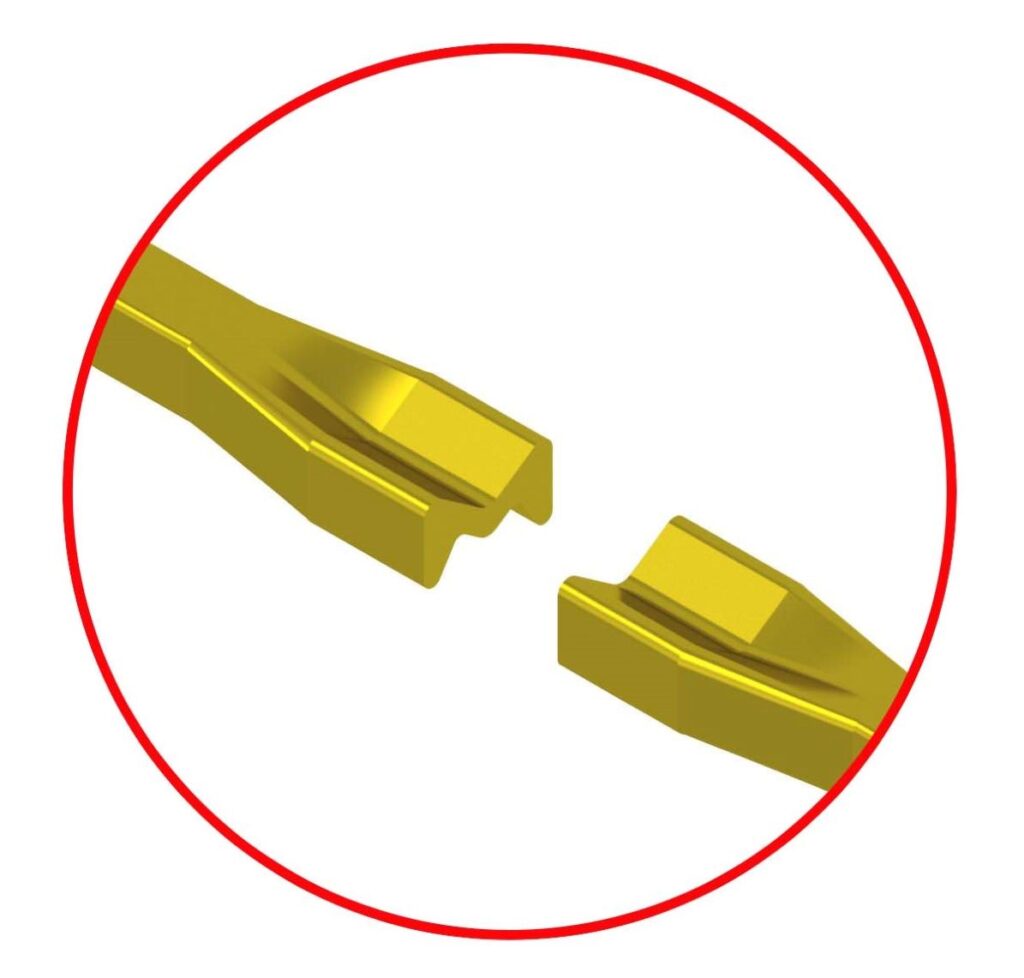
5.Crushing/dimpling
This type of forming is applied to the fitting section to provide retaining force to prevent the terminal from coming out of the housing.
Various shapes are available.
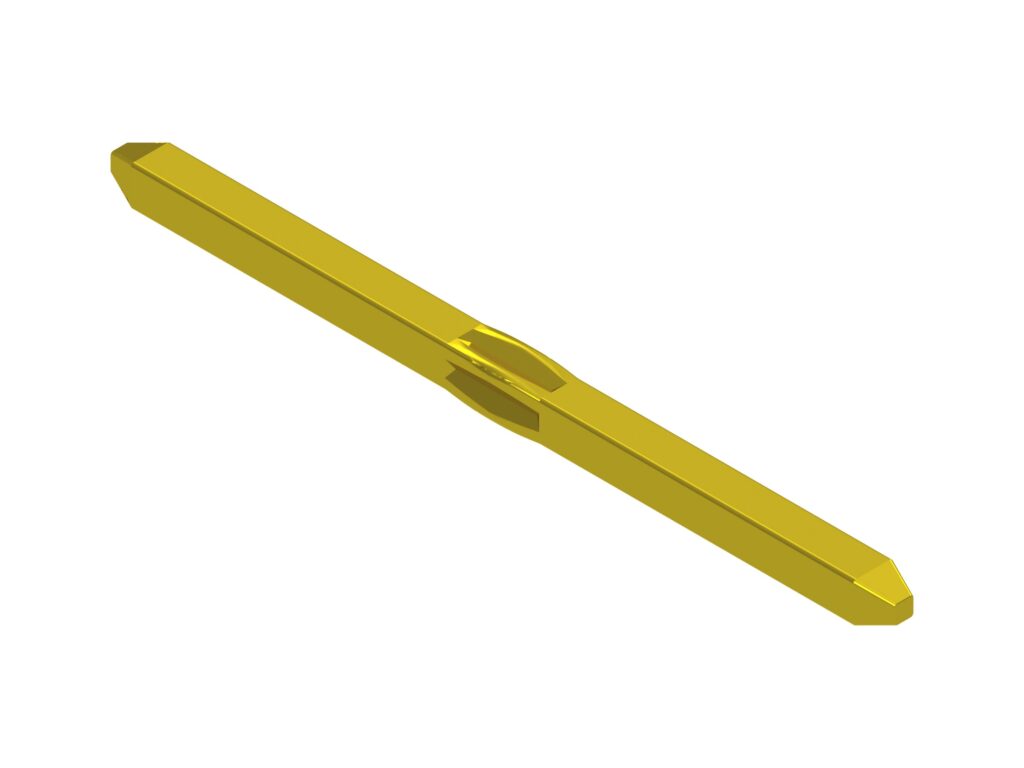
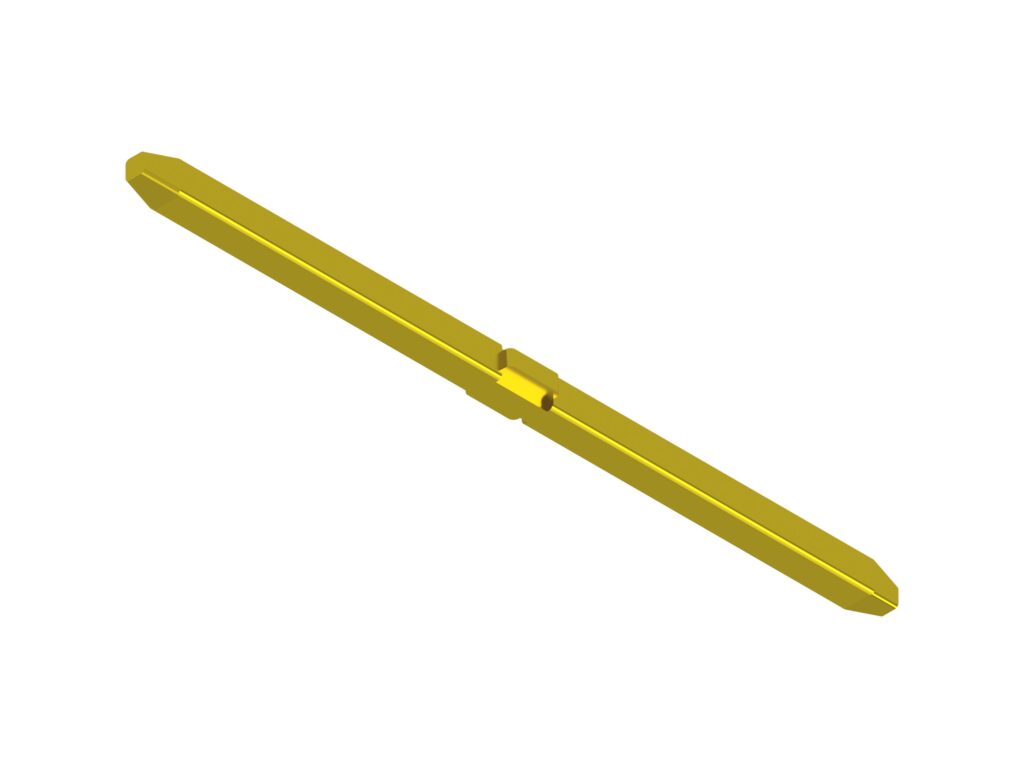
FINECS's connector terminals contributing to electrical contacts
FINECS’s connector terminals are critical components that bring about electrical contacts to products in a wide range of fields, including household appliances, digital equipment, mobile devices such as smartphones, computers, automobiles, industrial machinery, robots, medical equipment, and aviation parts.
A conductive failure of an electrical contact at even one connector terminal leads to a malfunction of the entire equipment;
therefore, connector terminals must always be of reliable quality.
FINECS has been manufacturing connector terminals/pins out of wire for more than 30 years using automatic pin processing machines produced in house, responding to a wide variety of customer needs. Having realized an automation system to minimize manpower through integrated in-house design and production of everything from the wire plating processes to terminal processing machinery, we are aiming to be a manufacturer that can achieve a world-class QCD performance through low-cost production and stable mass-productivity.
Furthermore, through the application of value engineering (VE), we are striving to manufacture the most valuable products in the world to meet customer needs with respect to connector terminal functionality.
FINECS will continue to contribute to our customers and society by providing unique FINE solutions for connector terminals/pins of all kinds and varieties.
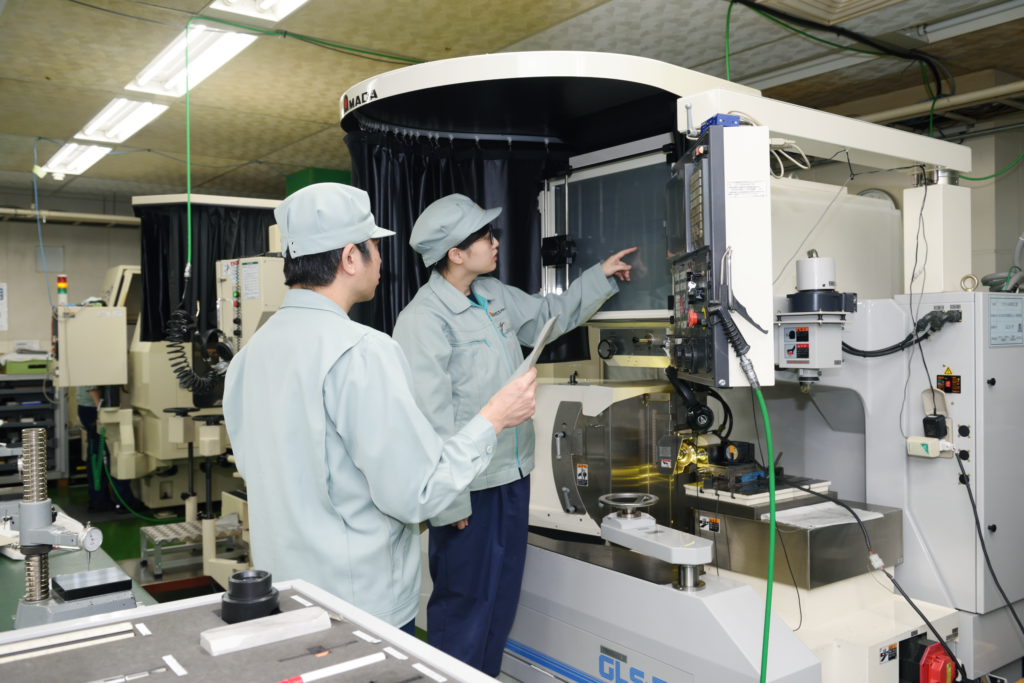
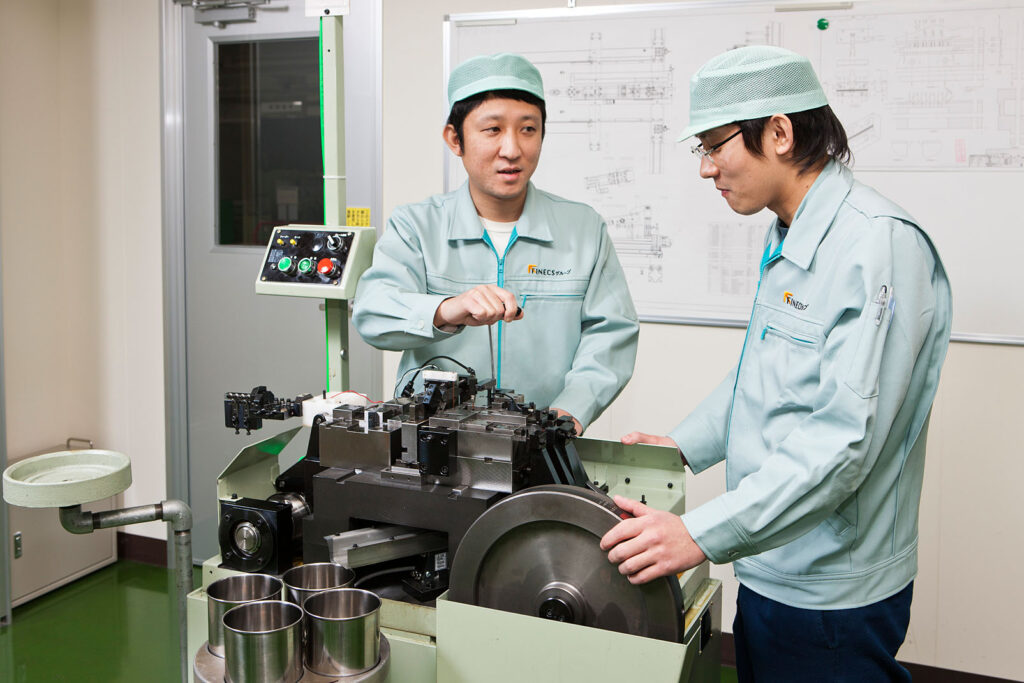
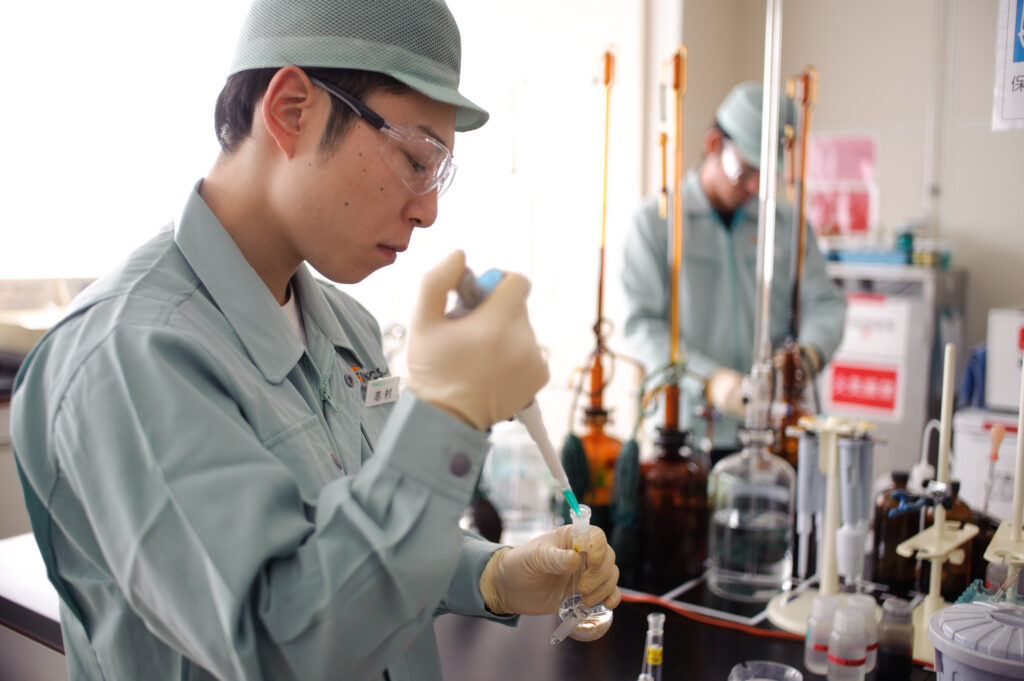